vibrating conveyors tray types
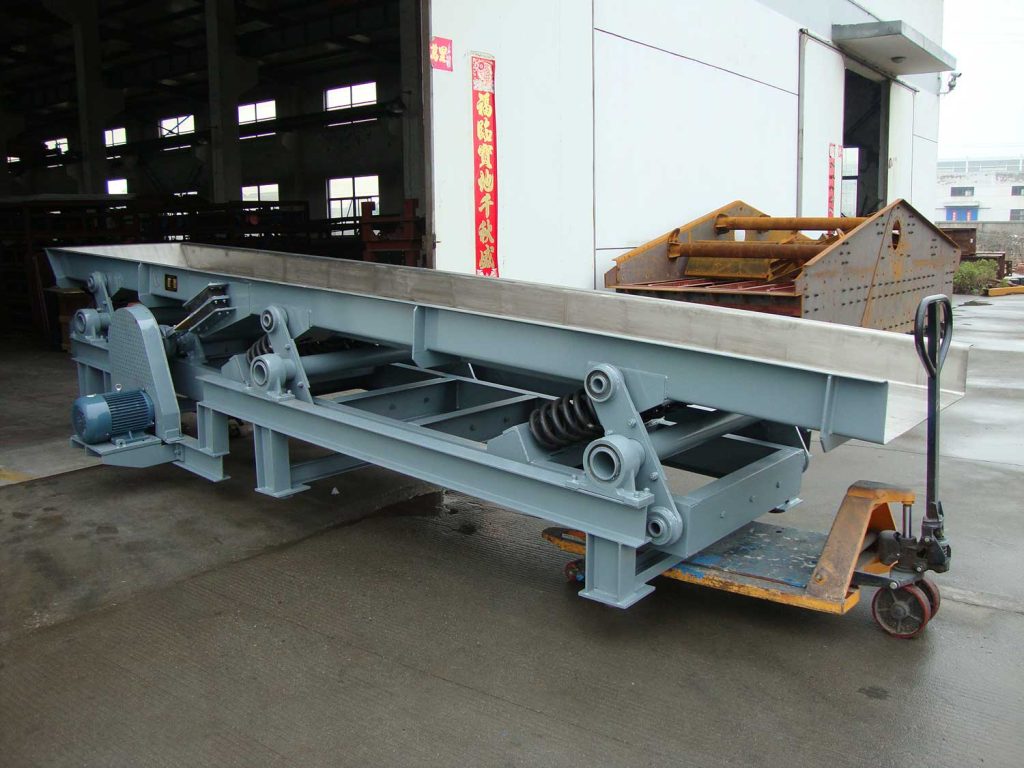
The shape, length, and width of vibrating conveyor trays are almost limitless. Feeder trays can be ordered with custom designs to satisfy the process application and material being conveyed, including flat, curved, vee-channel, and tubular designs. Intermediate discharge slide gates can be incorporated into some designs to allow for multiple discharge points along the tray length.
The vibrating conveyor trays are typically fabricated from mild steel or stainless steel. The latter is often used in food and pharmaceutical applications, while the former is for general purpose processing. Trays can be lined with abrasion-resistant steel, stainless, urethane, rubber, Teflon, and other coatings. Polishing the tray to various specified levels is another option to help keep material from adhering to the tray.
Generally, the vibrating conveyor trays are easy to access and clean, making it simpler to avoid cross-contamination of materials and decrease production downtime. Many trays have quick-release clamps that allow the tray covers or screens to be removed without tools.
10 tray types in a design of vibrating conveyors
Spigot / Circular Discharge
Ideal for feeding a Multihead Scale or with flexible fitting inlets and outlets
Adjustable End Piece
Ideal for feeding a Multihead Scale with products that don’t ‘carry well’ in flight, this will ensure an accurate supply of products typical for mixing applications.
Slotted Discharge
Ideal for product alignment @ 90° to freezers / ovens / dryers / roasters / chill blasters to deliver an even ‘curtain’ of product.
Scarf Discharge
Ideal for feeding an even spread of product @ 90° to the following interface, typically bucket elevators utilize this perpendicular option.
Flat Bottomed Design
Ideal for feeding a Multihead Scale or with flexible fitting inlets and outlets
Beveled Exit Discharge
Ideal for feeding a Multihead Scale or with flexible fitting inlets and outlets
Decreasing Width
Ideal for feeding an even spread of product @ 90° to the following interface, typically bucket elevators utilise this perpendicular option.
Tubular
Our Dustproof conveyor is the solution to alleviate issues caused by product leaching into the working environment. The tube design typically has a maximum filling capacity of approximately 50%.
V-shaped
Ideal for products that require a ‘pinched’ or very narrow discharge to the next process.
Rounded sides / semi-circular
Ideal for light, rounded items, particularly in the confectionery industry where sugar is used in many of the coating processes. As opposed to 90° angled sides, the rounded sides act as a ‘self-cleaning’ medium that eliminates the excessive build-up of sugars as the fresh product pushes the debris along with the product flow to be sieved out as necessary before packing.